Continuing on quality excellence: Promeco clears the second IRIS-audit with confidence
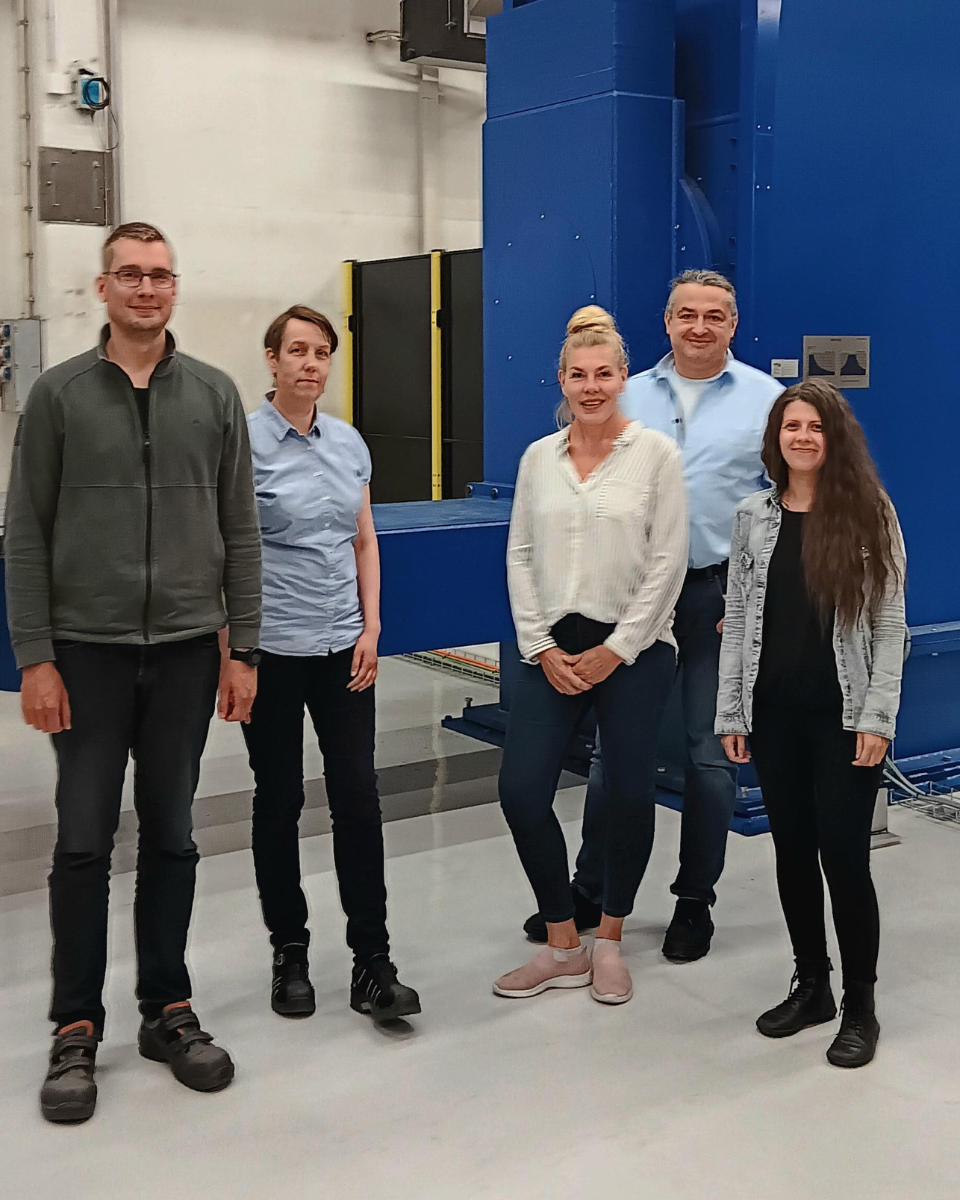
The second IRIS-audit in Promeco’s history was carried out on 31.7-1.8 at the Yrityspuisto factory in Kankaanpää by Bureau Veritas. The international IRIS certification is based on the ISO/TS 22163 standard, regarding quality management in the railway industry. The audit reviewed the process documentation throughout the production and supply chain, from sales and procurement to human resources, production and supply chain management. In addition, the auditors visited the production facilities to verify the compliance between the activities and the documented data and to identify areas for improvement. There are a total of eight IRIS-certified companies in Finland, of which Promeco has the most product scopes within the certification.
Going strong on bronze by small corrections
Promeco successfully passed the audit and continues meeting its goal by remaining on a strong bronze-level, similar to most certified companies in the industry. As a result of the audit, one non-conformance was detected with four development observations. In most areas Promeco achieved excellent or good results, all of which typical among the reference group.
The auditors’ clear overall impression was that Promeco’s understanding and expertise in the IRIS standard has increased. The auditors noted that few of the company-specific strengths are the management and employee commitment as well as the operations flexibility.
Two year trajectory resulting on multiple benefits
Initially, the certification process began at the end of 2021, followed by intensive efforts in documentation work and participating actively in workshops. As a result of the hard work, Promeco was audited and granted the certificate in October 2022. The benefits of the IRIS-required ways of working, which have now been in use for more than a year, can already be seen as increased process understanding and improved documentation practices. The process description has become more accurate, painting a better picture of what is actually being done. In this way, competence has been made more evident, improving the scalability of detected best practices. Resulting in many moments of enlightenment, the advanced documentation has brought into daylight things that have been done well and correctly already before. Improved and systematic measuring, on the other hand, have been great tools to efficiently demonstrate the development of processes, indicating the need for corrective actions in case the goals are not being achieved as desired.
Proper documentation is not only beneficial for Promeco’s internal processes, but also a solid part of customer-centric operating model. Documentation serves as a tool for quality assurance and supports proactive customer service when the information and documents requested by the customer are available immediately. Following the certified best practices results in a multiplication of benefits: as quality improves, complaints and consequently the amount of resources used to resolving them decreases for both parties. Systematic documentation ensures seamless continuity of processes even in the midst of changes, such as employees leaving the company.
Future prospects – extending the excellence
Moving forward, the first priorities are correcting the deviation and taking action regarding the observations. Continuous improvement being one of Promeco’s core values, already well functioning practices will also be gradually further optimized. In addition, updates have been made to ISO/TS 22163, which will be taken into account in the future actions. Next year, the audit will be carried out in accordance with the updated program.
With the IRIS-certification leading the way, the process thinking serves as an example also for other areas of business operations. One future goal for the company is to apply the lessons learned to its operations more extensively.